همانطور که همه ما می دانیم، ریخته گری سرمایه گذاری تولید می کندریخته گریبا دقت دقیق و پرداخت خوب. با این حال، در طول فرآیند تولید ازریخته گری سرمایه گذاری، بسیاری از عیوب ریخته گری رایج ممکن است. با توجه به تجربه مهندسی و تجهیزات پیشرفته خود، می توانیم با تجزیه و تحلیل علل، راهی برای جلوگیری از چنین مشکلاتی پیدا کنیم. در زیر چندین عیب رایج ریخته گری و علل و روش های پیشگیری از آنها را معرفی می کنیم. امیدواریم این مقاله برای مشتریان ما برای درک مشکلات مفید باشد و برای همکاران ما، این تجزیه و تحلیل می تواند به شما در جلوگیری از نقص احتمالی ریخته گری کمک کند.
سد زیرزمینی و سرد
1. شرح مشکل:
زیر ریختگی اغلب فاقد گوشت در دیواره نازک قالب یا دور از رانر داخلی است و لبه آن قوس شکل است. پارتیشن سرد به این صورت است که دو رشته فلز مذاب کاملاً با هم ذوب نشده اند و اتصالات آشکاری وجود دارد.
2. علت:
1) دمای ریختن فلز مذاب پایین و دمای قالب
2) سرعت ریختن آهسته است یا تنظیم دونده نامعقول است، جریان فلز بیش از حد طولانی است
3) ضخامت دیواره ریخته گری بسیار نازک است و جریان فلز مذاب ضعیف است
4) در هنگام ریختن قطع شود
3. اقدامات پیشگیرانه:
1) دمای ریختن فلز مذاب و دمای قالب را افزایش دهید
2) سرعت ریختن را افزایش دهید یا تعداد یا مساحت رانر داخلی را افزایش دهید تا جریان فلز مذاب کاهش یابد.
3) برای جلوگیری از قطع شدن در هنگام ریختن، هد فشار رایزر را افزایش دهید
انقباض
1. توضیح مشکل:
فقط با بررسی اشعه ایکس می توان آن را پیدا کرد. انقباض سطح را می توان با فلورسانس یا بازرسی رنگ آمیزی پیدا کرد. در موارد شدید، می توان آن را پس از شن و ماسه یافت.
2. علت:
1) ساختار ریخته گری غیر منطقی است و نقاط داغ بیش از حد یا خیلی بزرگ هستند
2) ظرفیت گرمایی بالابر ریختن کم است، که نمی تواند انجماد متوالی را تشکیل دهد، یا سر فشار کوچک است، که ظرفیت تغذیه را کاهش می دهد.
3) دمای قالب کم است، سرعت خنک کننده سریع است و کانال تغذیه مسدود شده است
3. اقدامات پیشگیرانه:
1) ساختار ریخته گری را بهبود بخشید و نقاط داغ را کاهش دهید
2) رایزر را به طور معقول تنظیم کنید، یا یک دنده تغذیه اضافه کنید که با روش های پردازش قابل برداشتن باشد، هد فشار را افزایش دهید، به طوری کهریخته گری سرمایه گذاریمی توان به طور متوالی تحت تأثیر یک سر فشار خاص جامد شد
3) دمای ریختن و دمای قالب را به طور مناسب افزایش دهید تا سرعت خنک شدن کاهش یابد
ترک داغ
1. شرح مشکل:
ترک های نامنظم بین دانه ای روی سطح یا داخل ایجاد می شود و سطح اکسید می شود. می توان آن را پس از تمیز کردن شدید شن و ماسه مشاهده کرد و فقط پردازش ملایم یا بازرسی نفوذ یافت می شود.
2. علل:
1) مربوط به ترکیب آلیاژ است، محتوای کربن و سیلیکون بالا است، محدوده دمایی فاز مایع-جامد بزرگ است و ترک گرم آسان است.
2) دمای قالب پایین، قابلیت عقب نشینی ضعیف و سرعت خنک شدن سریع
3) ضخامت ریخته گری بسیار متفاوت است و فیله انتقال بسیار کوچک است
3. اقدامات پیشگیرانه:
1) برای آلیاژها یا فولادهایی که مستعد ترک های داغ هستند، میزان کربن و سیلیکون آنها باید تا حد امکان تا حد وسط و پایین کنترل شود.
2) دمای قالب را در حین ریختن افزایش دهید، سرعت خنک شدن قالب را کاهش دهید یا مقاومت پوسته قالب را کاهش دهید.
3) دنده های فرآیند ضد ترک را در محل اتصال به ضخامت قطعات ریخته گری اضافه کنید یا فیله های انتقالی را افزایش دهید.
کراک سرد
نام و مشخصات:
ترک های نافذ پیوسته روی ریخته گری وجود دارد. یک سطح براق یا یک سطح کمی اکسید شده در محل شکستگی ظاهر می شود.
علل
1. در طول فرآیند خنک سازی ریخته گری، انقباض مانع می شود و در نتیجه تنش حرارتی و تنش تغییر فاز ایجاد می شود و این تنش ها از استحکام ماده در حالت الاستیک بیشتر می شود و باعث شکستگی می شود.
2. در فرآیند تمیز کردن پوسته، برش دروازه، رایزر یا در حین تنظیم، ریخته گری با تنش پسماند تحت فشار خارجی قرار می گیرد تا باعث شکستگی شود.
روش های پیشگیری
1. دنده های سفت کننده را در ترک های سرد اضافه کنید تا قابلیت عقب نشینی شکل را بهبود بخشد، در نتیجه مقاومت در برابر انقباض و استرس ریخته گری را کاهش دهید.
2. در فرآیند پس از ریخته گری، از ضربه شدید بین ریخته گری ها اجتناب کنید.
منفجره
نام و مشخصات
سوراخ های آشکار یا نامحسوس با سطح داخلی صاف روی ریخته گری وجود دارد.
علل
1. نفوذپذیری هوای ضعیف پوسته قالب، که باعث می شود گاز موجود در حفره در حین ریختن خیلی دیر تخلیه شود.
2. شلیک ناکافی شکل پوسته، در نتیجه حذف ناکافی بقایای مواد قالب و مواد مولد گاز در مواد پوسته.
3. محتوای گاز مایع فلزی بسیار زیاد است و باعث اکسیداسیون ضعیف می شود.
4. تنظیم سیستم ریختن غیر منطقی است و باعث می شود گاز انسانی در ریختن دخیل باشد.
روش های پیشگیری
1. نفوذپذیری هوای پوسته را بهبود بخشید و در صورت لزوم دریچه هایی اضافه کنید.
2. گلوله کاملا شلیک شده.
3. بهبود روش های اکسیداسیون.
4. بهبود سیستم دروازه.
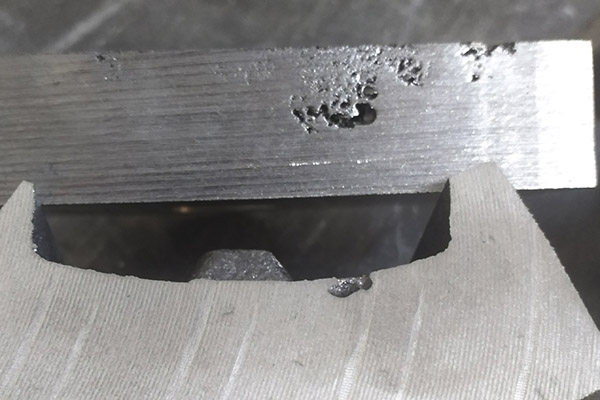
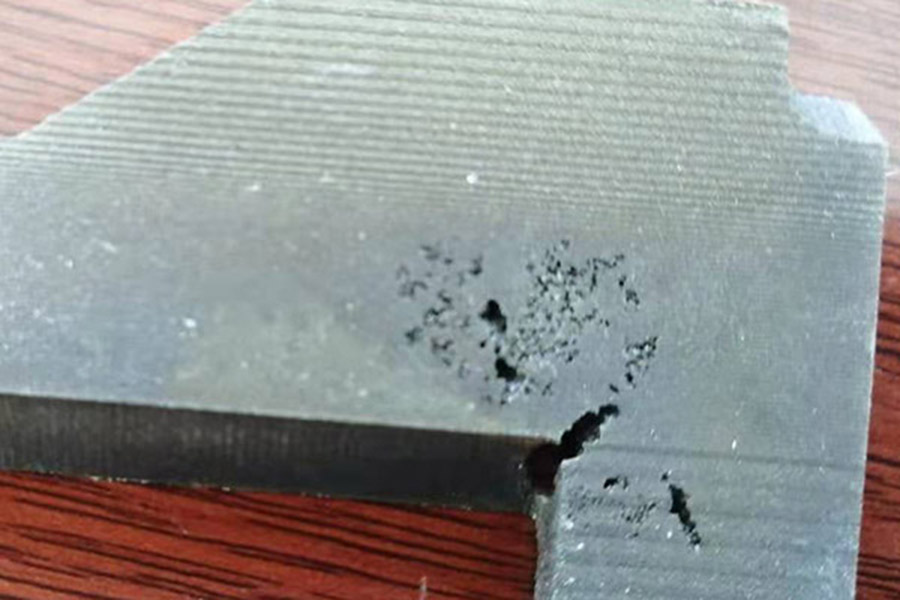
ریخته گری گودال
نام و مشخصات
بر روی سطح ریخته گری گودال های نقطه مانند متراکمی وجود دارد.
علل
1. هنگامی که اتیل سیلیکات به عنوان چسب استفاده می شود، هیدرولیز ناقص در فرآیند پوشش قرار دارد، رطوبت نسبی داخل ساختمان بسیار کم است، به طوری که هیدرولیز نمی تواند بیشتر هیدرولیز شود، و "یخ زدگی سفید" پس از برشته کردن رسوب می کند.
2. هنگامی که از شیشه آب به عنوان چسب استفاده می شود، نمک باقیمانده در پوسته قالب با فلز مذاب واکنش داده و گودالی را تشکیل می دهد.
3. فلز مذاب بد اکسیده شده یا سرباره در حین ضربه زدن تمیز نمی شود.
روش های پیشگیری:
1. هنگام استفاده از اتیل سیلیکات به عنوان چسب، مقدار آب اضافه شده را به طور مناسب افزایش دهید و رطوبت نسبی استودیو رنگ را افزایش دهید تا هیدرولیزهای ناقص باقیمانده را به حداقل برسانید.
2. هنگام استفاده از لیوان آب به عنوان چسب، پوسته را پس از موم زدایی با آب اسیدی تمیز کنید.
3. پوشش سطح را به عنوان بایندر به سل سیلیس تغییر دهید.
4. در هنگام ذوب، اکسیداسیون و حذف سرباره را تقویت کنید.
ریخته گری سوراخ زیر جلدی
نام و مشخصات
پس از صیقل دادن سطح ریخته گری، لکه های سیاه ریز ظاهر می شوند. این پدیده بیشتر درفولاد ضد زنگ نیکل کرومl.
علل:
1. مواد بازیافتی بیش از حد در طول مذاب فلز استفاده می شود، یا مواد بازیافتی به درستی درمان نشده اند.
2. در طی فرآیند ذوب، فلز مذاب اکسید می شود یا فلز مذاب گاز را جذب می کند و در نتیجه اکسیداسیون ناکافی است.
3. محتوای ناخالصی مواد پوسته خیلی زیاد است یا عامل پیوند و فلز مذاب واکنش شیمیایی دارند.4. تنظیم غیر منطقی سیستم دروازه.
روش های پیشگیری:
1. مقدار مواد بازیافتی را کنترل یا کاهش دهید، و مواد بازیافتی باید بعد از دمیدن شن و یا شات بلاست استفاده شود.
2. فرآیند ذوب را به شدت کنترل کنید و اکسیداسیون را تقویت کنید.
3. از کوراندوم ذوب شده، ماسه زیرکون و سل سیلیس یا رنگ اتیل سیلیکات استفاده کنید.
4. سعی کنید از روش تزریق پایین برای ریختن و افزایش سوراخ های هوا استفاده کنید.
شن و ماسه چسبنده
نام و مشخصات
یک لایه ماسه چسبنده در نزدیکی رانر یا داخل قالب ریخته گری وجود دارد و پس از دمیدن ماسه، سوراخ ها یا گودال های برجسته وجود دارد.
علل
1. محتوای ناخالصی پودر نسوز مورد استفاده در لایه سطحی پوشش بسیار زیاد است و این ناخالصی ها با فلز مذاب واکنش داده و یک یوتکتیک با نقطه ذوب پایین ایجاد می کنند.
2. دمای ریختن خیلی زیاد است، به ویژه گریدهای فولادی حاوی Al، Ti و سایر عناصر، که باعث واکنش شیمیایی بین فلز مذاب و سیلیس می شود.
3. تنظیم سیستم دروازه غیر منطقی است و مقدار زیادی فلز مذاب از طریق رانر داخلی جریان می یابد و باعث گرمای بیش از حد موضعی می شود.
روش های پیشگیری
1. به جای ماسه سیلیسی از یشم فولاد ذوب شده یا ماسه زیرکون استفاده کنید و سعی کنید از شیشه آب به عنوان چسب استفاده نکنید.
2. دمای ریختن را به طور مناسب کاهش دهید.
3. یک دونده داخلی برای تنظیم تعادل گرما و کاهش گرمای بیش از حد موضعی اضافه کنید.
دیلاتانت
نام و مشخصات
تورم موضعی در صفحه بزرگتر ریخته گری، این پدیده در هنگام استفاده از لیوان آب به عنوان چسبنده آشکارتر است.
علل
1. ساختار ریخته گری غیر منطقی است و مساحت صفحه بیش از حد بزرگ است.
2. پوسته در دمای بالا استحکام کمی دارد و نمی تواند فشار فلز مذاب را تحمل کند.
روش های پیشگیری
1. ساختار را بهبود بخشید، دنده های فرآیند یا سوراخ های پردازش را در هواپیما اضافه کنید.
2. هنگام ساخت پوسته از مواد پوسته ای با ناخالصی کمتر و نسوز زیاد استفاده کنید و یا ضخامت پوسته را افزایش دهید.
سرباره
نام و مشخصات
سرباره یا سایر مواد زائد در داخل یا سطح ریخته گری وجود دارد. آخال های داخلی باید توسط اشعه ایکس یا بازرسی مغناطیسی شناسایی شوند.
علل
1. مواد سرباره خیلی نازک است و قبل از ضربه زدن تمیز نمی شود.
2. ضایعات روی محفظه ضربه زنی بوته قبل از ضربه زدن تمیز نشده و به داخل فلز مذاب آورده شده است.
3. در هنگام ریخته گری، نگهداری سرباره خوب نیست و سرباره با فلز مذاب وارد حفره می شود.
روش های پیشگیری
1. ترکیب مواد سرباره را قبل از ضربه زدن تنظیم کنید تا ویسکوزیته مواد سرباره افزایش یابد و حذف سرباره آسانتر شود.
2. برای جلوگیری از وارد کردن ناخالصی ها به فلز مذاب در ملاقه، زباله های موجود در قسمت جلوی فولاد را تمیز کنید.
3. قبل از ریخته گری، مذابفلز ریخته گریبرای تسهیل شناور شدن سرباره باید به طور مناسب آرام بخش شود.
4. یک ملاقه ریختن قوری با درب سرباره یا فیلتر سرامیکی بردارید.
کربن زدایی
نام و مشخصات
محتوای کربن لایه سطحی ریخته گری کمتر از ماتریس است.
علل
1. در طول ریخته گری، دمای فلز مذاب و قالب بالا است و سرعت انجماد ریخته گری کند است.
2. عمق لایه کربن زدایی به جو محیط خنک کننده ریخته گری مربوط می شود. هر چه غلظت اتمسفر اکسید کننده بیشتر باشد، کربن زدایی جدی تر است.
روش های پیشگیری
1. دمای ریخته گری و دمای قالب را به طور مناسب کاهش دهید تا سرعت خنک شدن را افزایش دهید.
2. به طور مصنوعی یک فضای کاهنده در اطراف قالب ایجاد کنید، مانند افزودن کربنات باریم و پودر زغال چوب به قالب.
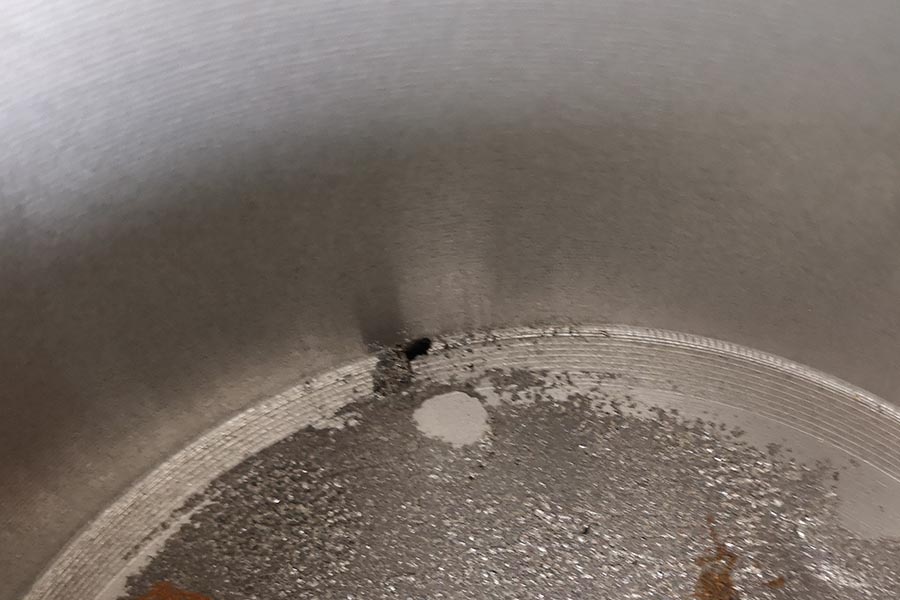
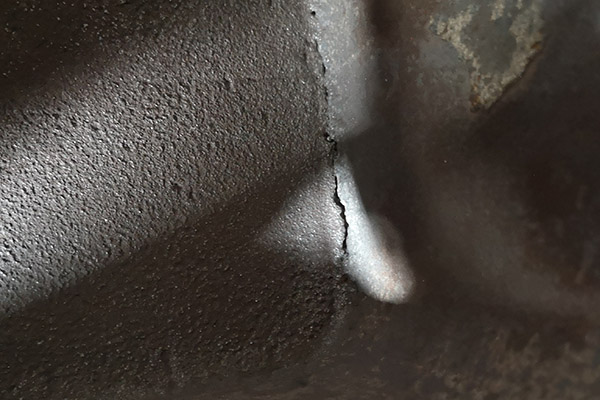
زمان ارسال: ژانویه 22-2021